Dedicated to improving hygiene standards ...
Near the German border lies one of Arla Foods' most extensive white cheese production facilities. Dedicated to continually improving hygiene standards, Arla seeks the expertise of JEROS to design a washing solution for the white cheese Alpma line, which is responsible for cutting and packaging at the Kruså plant.
Arla Foods is a major international dairy company from Denmark, and the white cheese plant in Kruså is a crucial part of their operations. This plant produces top-quality white cheese, which helps uphold Arla's global reputation for excellence in dairy products, including milk, cheese, butter, yogurt, and cream.
You may know about the dairy's high-quality, nutritious products under well-known brands such as Arla, Lurpak, and Castello. Additionally, Arla Foods caters to various consumer needs with a wide range of products, including organic options, lactose-free items, and high-protein dairy products. This variety shows that Arla Foods values and meets your unique needs.
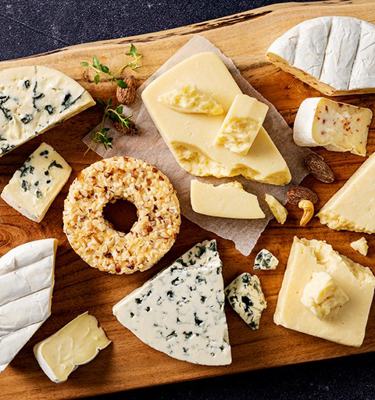